Spin your Success!
Our high-precision and custom-designed motor, belt-driven and special spindles provide exactly the right movement for your business.
With more than 50 years of experience.
Tailored to your specific application.
The Right Solution for Every Spindle Application
We are by your side: from development to manufacturing, from engineering to service. And we look forward to your project and your inquiry.
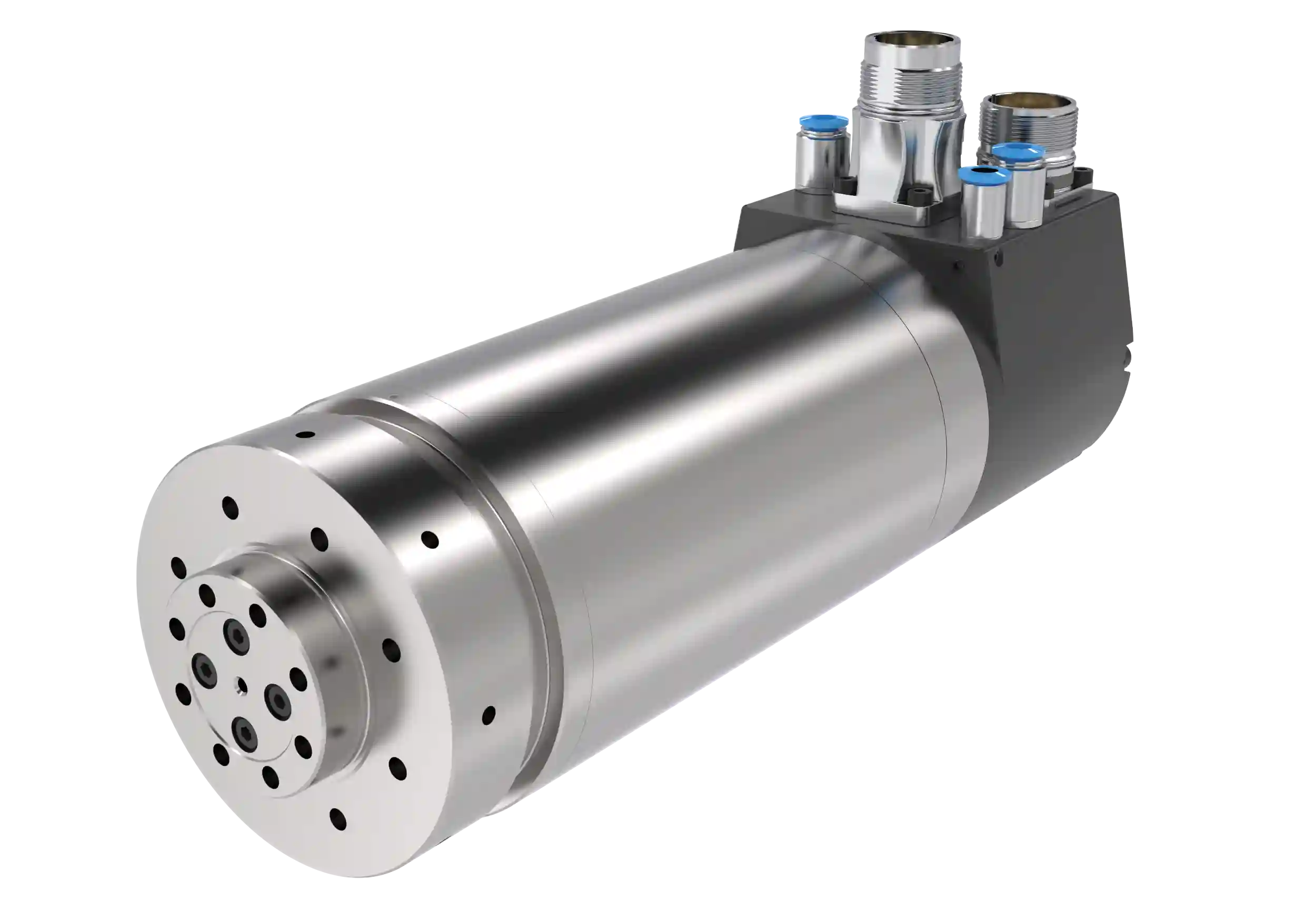
Dressing Spindles
Dressing spindles are powerful motor spindle systems designed to the latest standards - specifically for dressing with rotating tools. A modular system ensures that the spindles can be easily assembled in the required configuration. The integration of rotary encoders and chamfer detection is always possible.
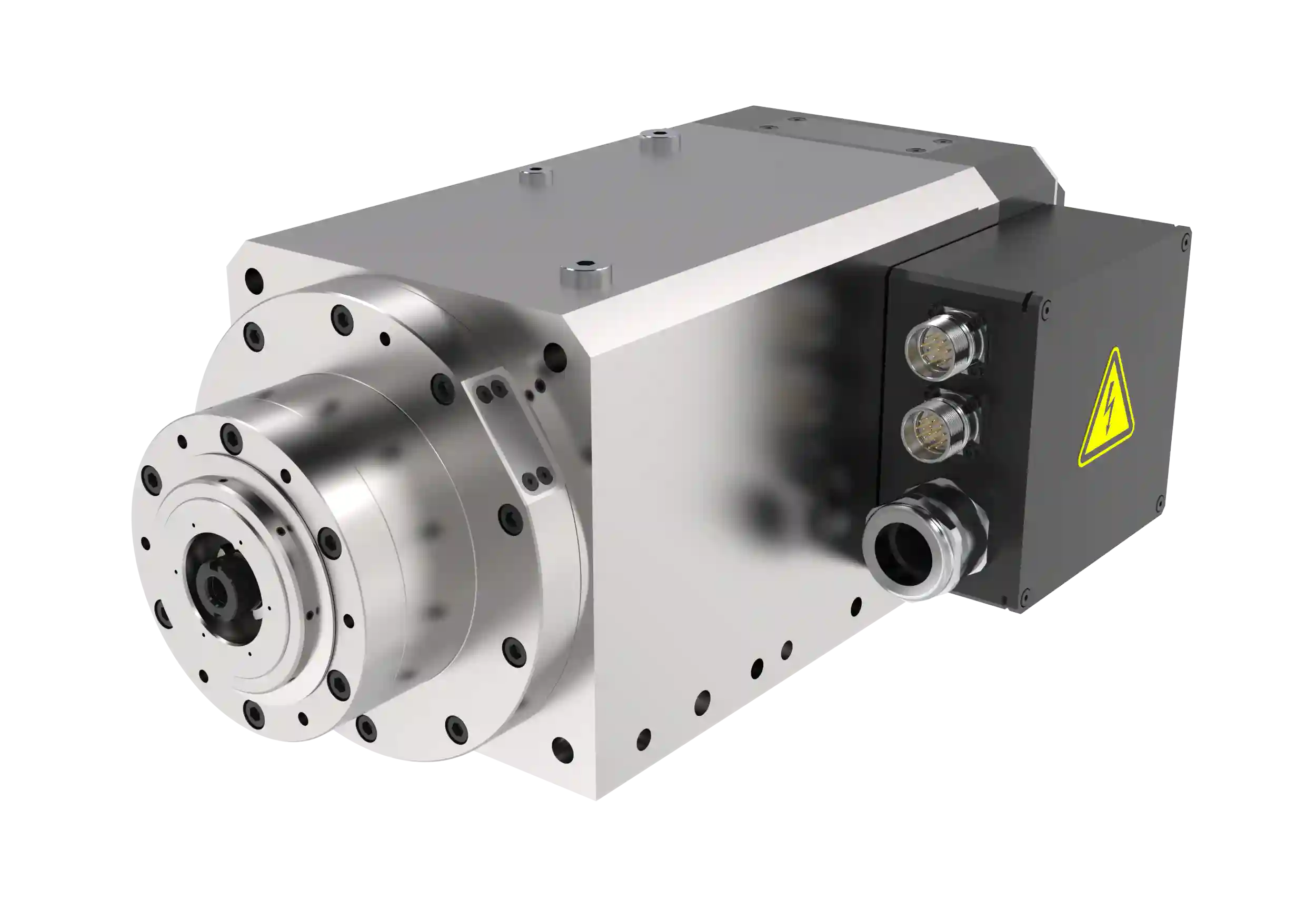
Milling Spindles
Our milling spindles are equipped with HSK tool clamping systems. However, other clamping methods are also possible. Tool clamping and release can be performed manually or automatically. The smooth operation of the spindles is achieved through a rigid design and an optimal balancing process. The spindles can be used both horizontally as well as vertically.
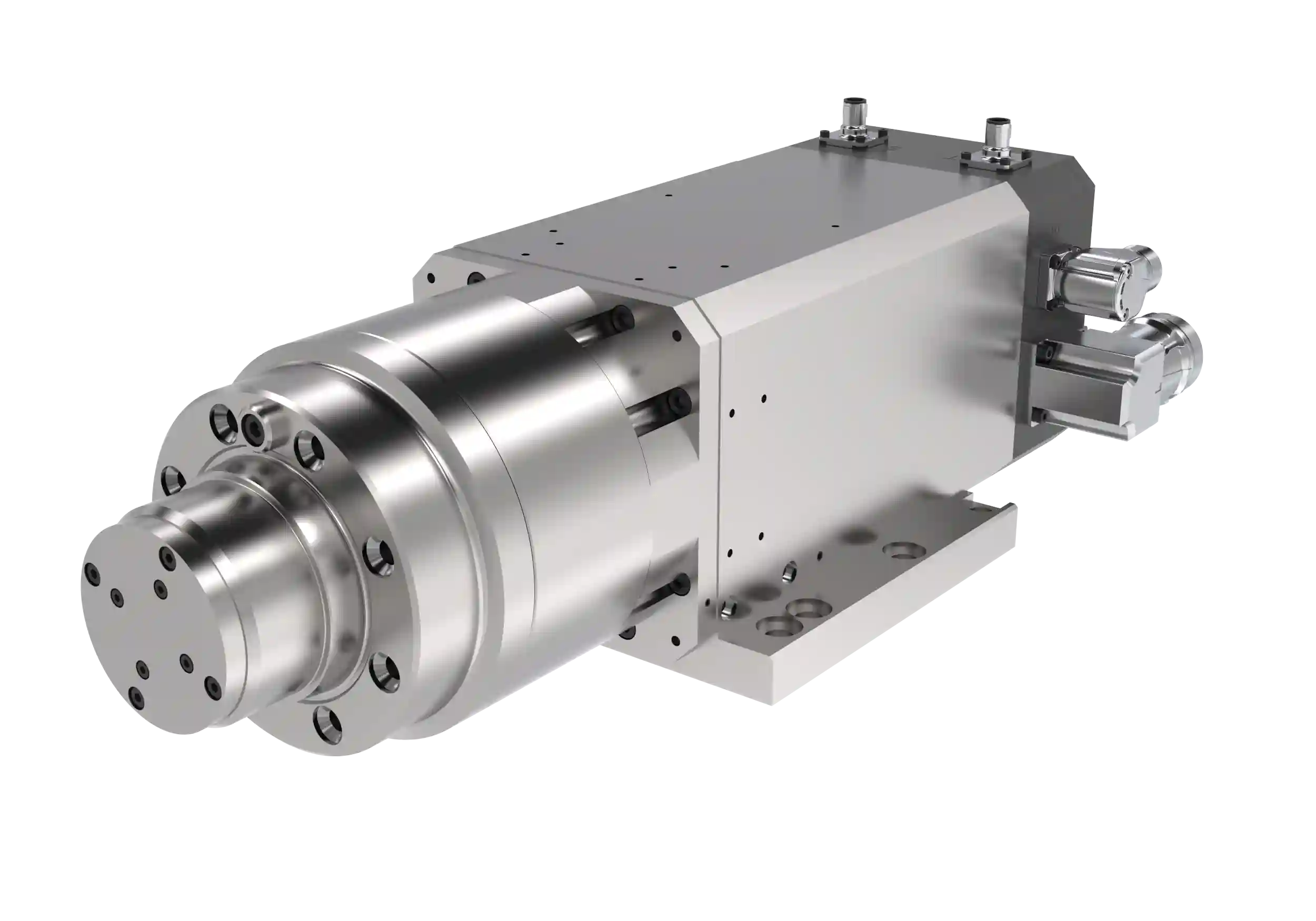
Grinding Spindles
Special materials are used in the manufacturing of our grinding spindles to ensure high dimensional stability even under extreme operating conditions. For the bearing, only high-precision bearings under preload are fitted. The true-running accuracy at the receiving taper is <0.002 mm. Automatic balancing systems as well as various sensors for condition monitoring can be integrated.
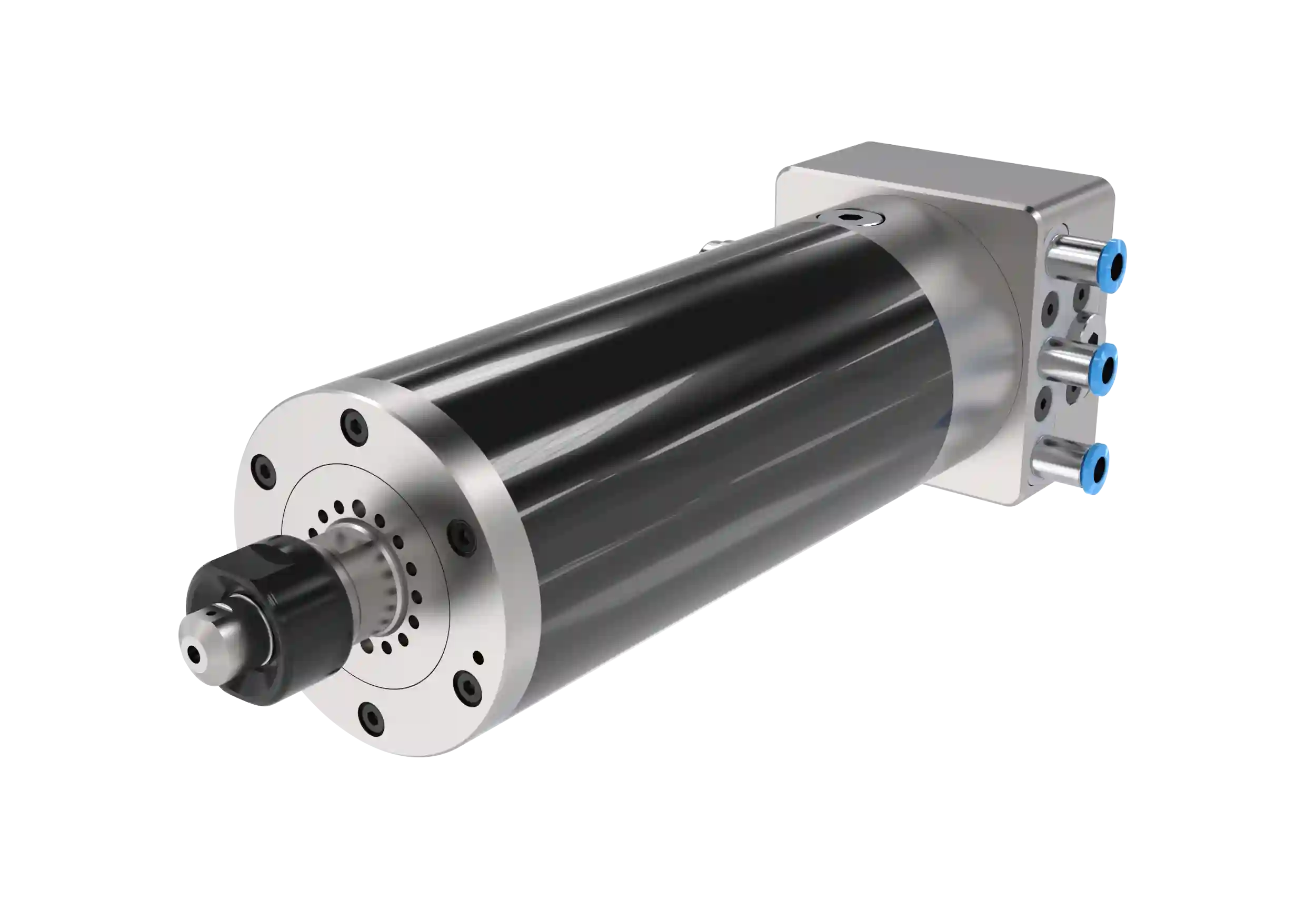
EDM Spindles
Special materials are used in the manufacturing of our grinding spindles to ensure high dimensional stability even under extreme operating conditions. For the bearing, only high-precision bearings under preload are fitted. The true-running accuracy at the receiving taper is < 0.002 mm. Automatic balancing systems as well as various sensors for condition monitoring can be integrated.
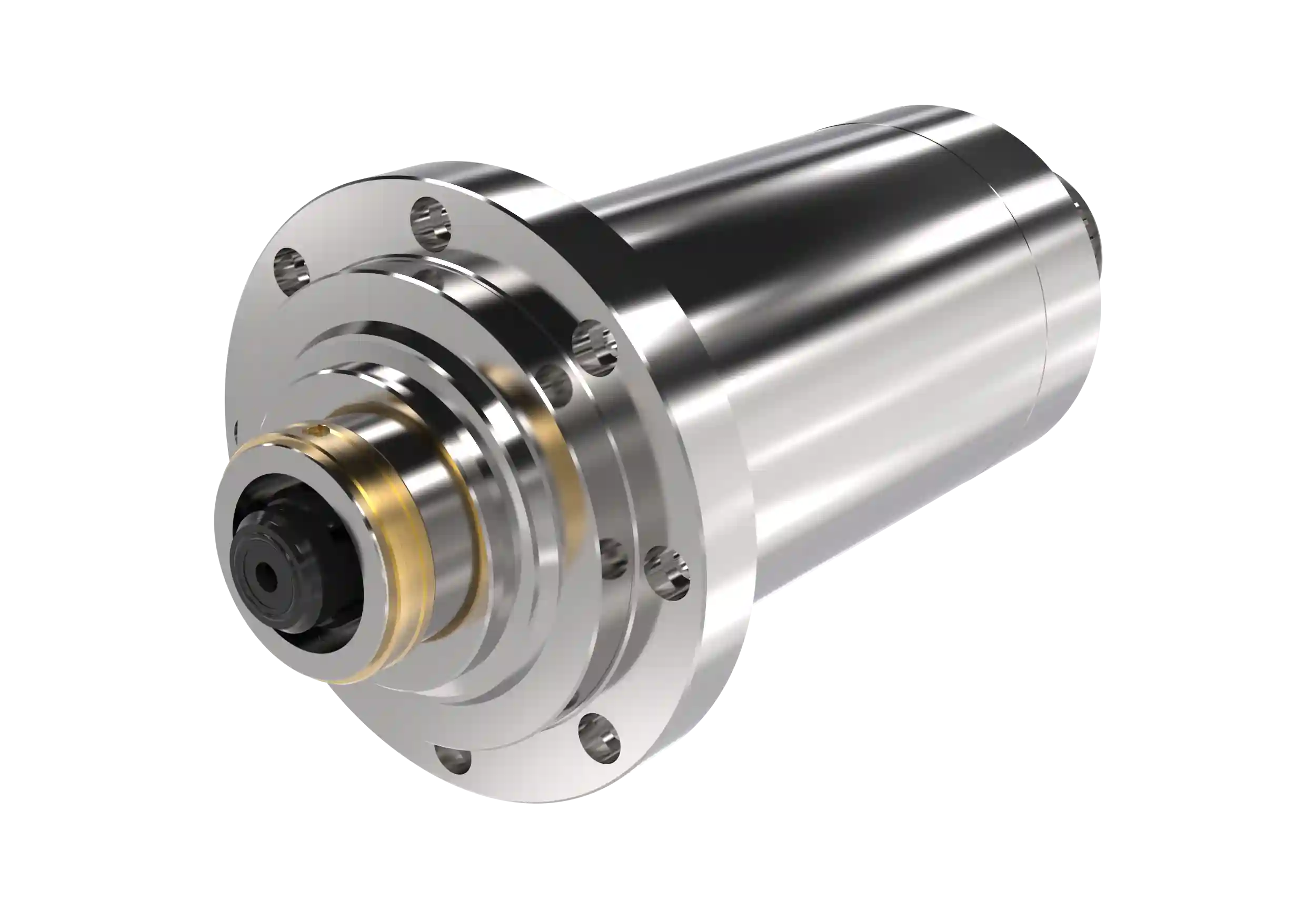
Drilling Spindles
Drive is provided by compact, powerful synchronous and asynchronous motors. We only use high precision bearings that are preloaded. Smooth spindle operation is achieved by a rigid structure designed to withstand high axial forces.
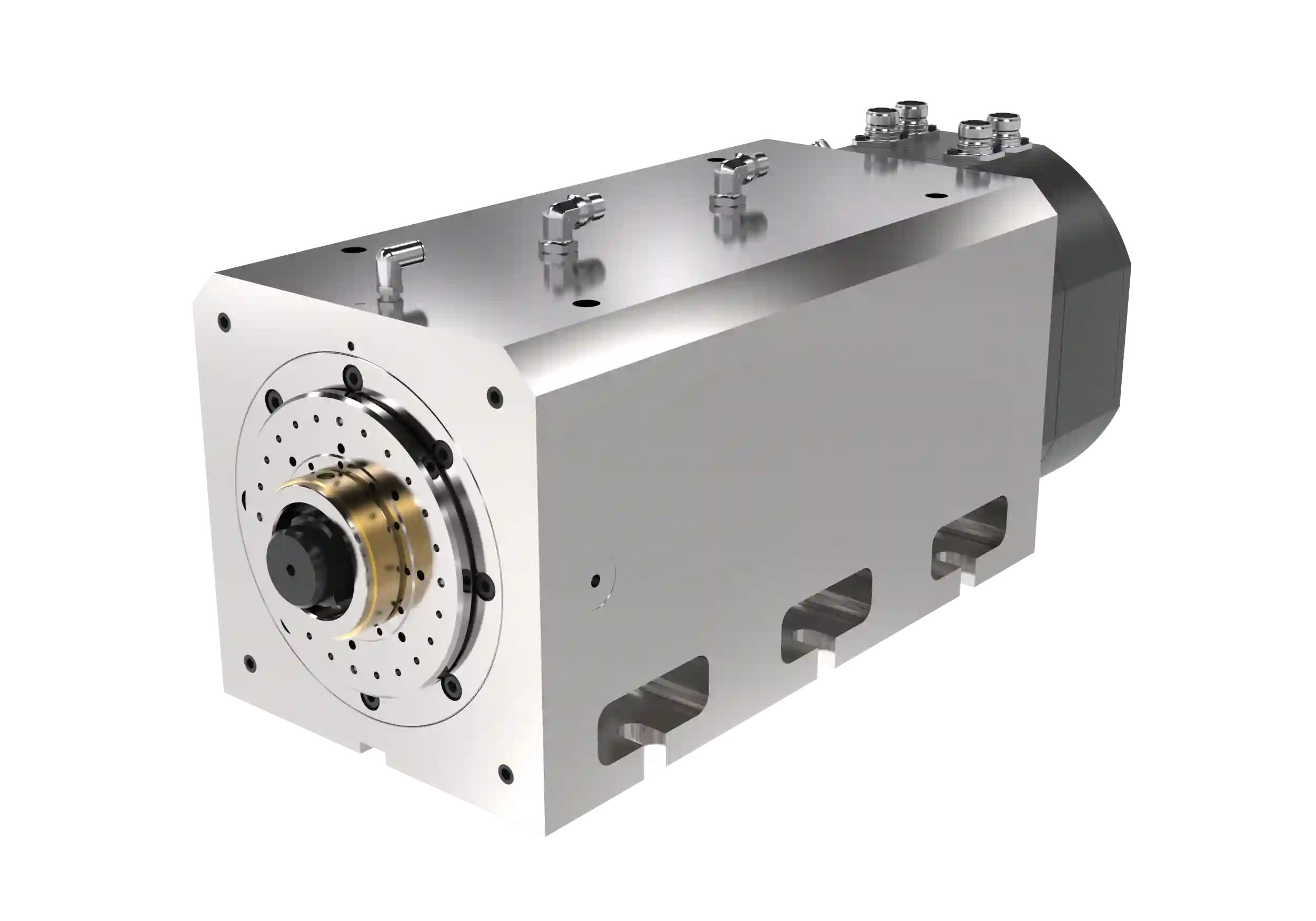
Friction Welding Spindles
Due to high process reliability, our spindles can optimally join components by friction and force, which are achieved by a rigid structure and an ideal balancing process. A wide range of materials such as steel, copper, aluminum, cast iron, stainless steel and others can be joined using friction welding.
> 50 Years
of Experience
in engineering und spindle technology
> 1000
Spindles
manufactured every year
80 %
Custom-Designed
according to customer requirements
Your Advantages of Working With Spindle Masters
Our customers particularly appreciate the quality and focus of our advice and execution. That is why our quality management is also ISO 9001 certified. But we offer much more:
With our expertise as specialists in spindle technology and the flexibility of a medium-sized company, we can provide comprehensive support for all aspects of spindle solutions.
Production From Batch Size 1
We offer customized solutions even in small quantities. This makes us the ideal partner for innovative and specialized applications.
Extensive Engineering
With our expertise and technical capabilities, we can support you in areas such as simulation, thermal measurement and rigidity analysis.
Service and Repair
We professionally refurbish defective spindles with new parts, meeting the same acceptance criteria as for new spindles.
Spindle Hotel
We are happy to store your spindles to prevent damage due to downtime. The warranty period only starts from the date of dispatch.
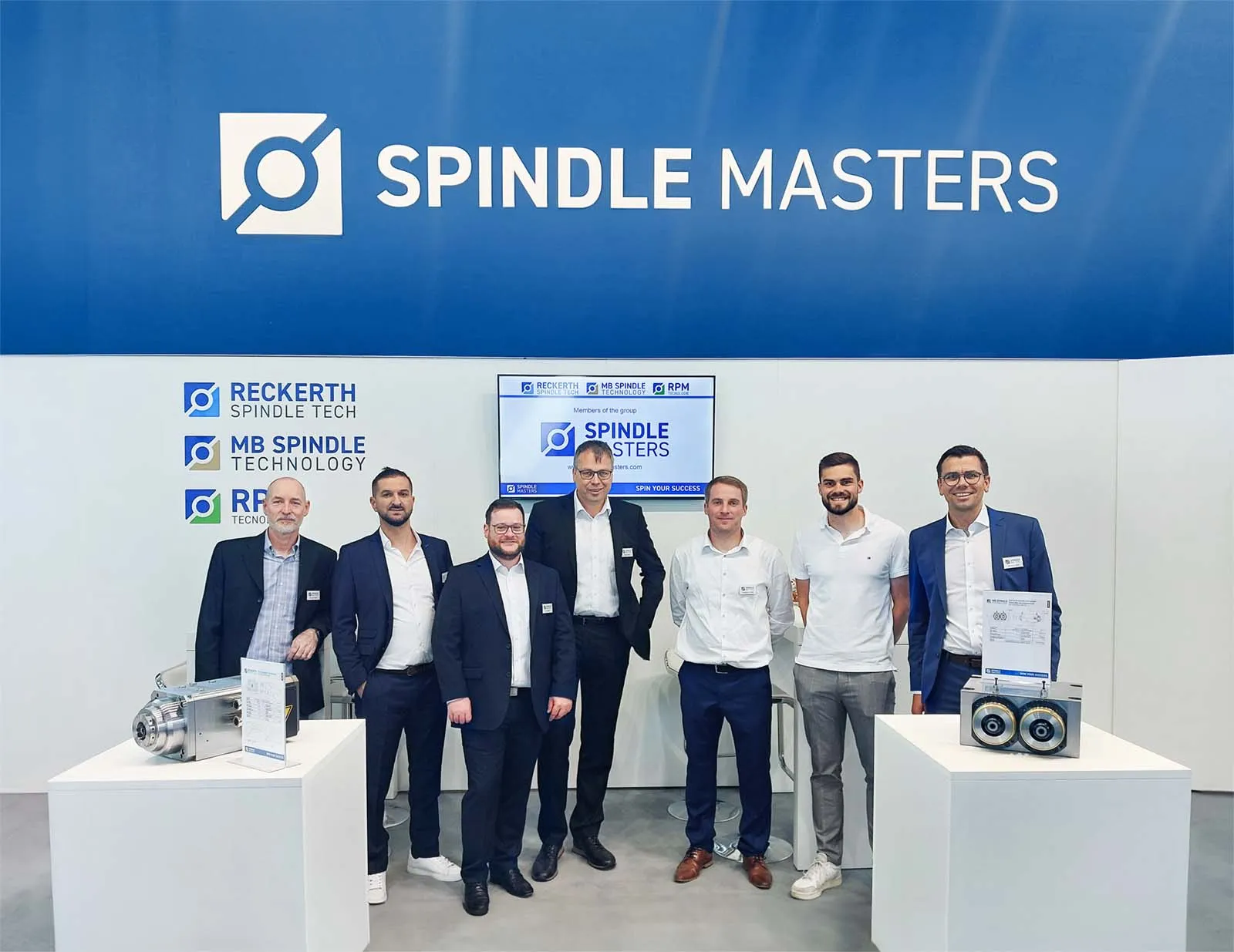
Spindle Masters is driven by experienced and innovative teams from three internationally recognized quality suppliers. We are specialists in the development and production of motor spindles, belt-driven spindles and special spindles. Our shared ambition and passion? Spin your Success!
With our locations in Filderstadt (GER), Röllbach (GER) and Pontoglio (ITA), we offer a wide range of services - both standardized model series as well as individual and innovative solutions.
For you, this means that we can work flexibly and efficiently thanks to our co-operation within the network. At the same time, you benefit from our extended pool of expertise. These benefits make Spindle Masters the ideal partner for your spindle solution.
With our medium-sized DNA, we emphasize direct channels, clear communication and binding agreements. We look forward to getting in touch with you personally.
Our shared roadmap
This is how we process both your manufacture and repair requests accurately and quickly:
Advising
We come together to discuss the key points of your spindle project.
Design & Engineering
We then develop a customized concept - due to our modular system with maximized efficiency. The core element is the dimensioning of the bearing system which is tailored to your specifications.
Adjustments & Approval
You can now integrate our CAD model into your machine design, allowing a detailed review of the setup. After commissioning, any necessary adjustments are made and an approval drawing is produced.
Manufacturing
We immediately start production after receiving your approval. Using our extensive range of machinery, we manufacture the individual components with high precision and then assemble them accurately in our assembly process. Lastly, the spindle is commissioned on the test bench.
Quality Control
Every spindle is thoroughly examined and the results are documented in an approval report. Our Spindle Master quality is not only ISO 9001 certified but comes from our more than 50 years of experience.
Analysis
The spindle requiring repair is delivered, dismantled and examined. All individual rotation-symmetrical components are checked and calibrated utilizing state-of-the-art measuring technology. A detailed repair and action report summarizes the results together with a cost estimate.
Repair
Upon approval of the costs, the problem is addressed and solved immediately, even for spindles of other manufacturers.
Thanks to our company-internal grinding and turning shop, the repair time is reduced to a minimum.
Final Assembly
As a result of the spatial separation of damage analysis and final assembly in the clean room, we guarantee highest quality standards during the handover.
Quality Control
The fine-tuning of the balancing and test runs with protocols for the customer are carried out in this phase. In a separate break-in room, we run every spindle up to the final speed prior to the delivery to the customer.
Warranty
The quality of a repaired spindle corresponds with that of a new spindle. A repaired spindle carries a warranty of 6 months.
Which project can we help you with?
Individual advice on a personal level is very important to us. Thank you for providing us with your contact details and further information about your spindle project. We will get back to you as soon as possible and look forward to talking to you.
Frequently Asked Questions:
We produce exclusively in Europe at our production sites in Germany (Filderstadt/Baden-Württemberg and Röllbach/Bavaria) as well as in Italy (Pontoglio/Brescia region).
We look forward to hearing from you via the contact form or directly at info@spindlemasters.com or +49 0711 722579-0.
We can specify our recommendation based on your information regarding the tool interface and HSK taper, the performance data, the speed range as well as the application area of the spindle project.
The respective spindle is delivered, dismantled and analyzed. The results are summarized in a detailed repair and action report with a cost estimate. Once the costs have been approved, the problem solving begins immediately (also for spindles from other manufacturers). Thanks to our company-internal grinding and turning shop, repair times are reduced to a minimum. The quality of a repaired spindle is equivalent to that of a new spindle.
We need information on the serial number, spindle type and customer details.
The quality of a repaired spindle is equivalent to that of a new spindle. All individual components of the spindle are inspected and adjusted after disassembly. During the final inspection, a repaired spindle must meet all the tolerances of a new spindle.
Spindles from all manufacturers can be repaired and refurbished.
The spindle hotel offers a professional storage space for your spindle with high-quality standards. Our experienced technicians regularly inspect and measure the spindle. During these inspections, the spindle is operated at its maximum speed limit. By storing your spindle in our spindle hotel, we can react quickly to your needs and provide you with a replacement spindle in a timely manner if required.
Do you have any further questions?
Please feel free to contact us directly. We look forward to your inquiry!